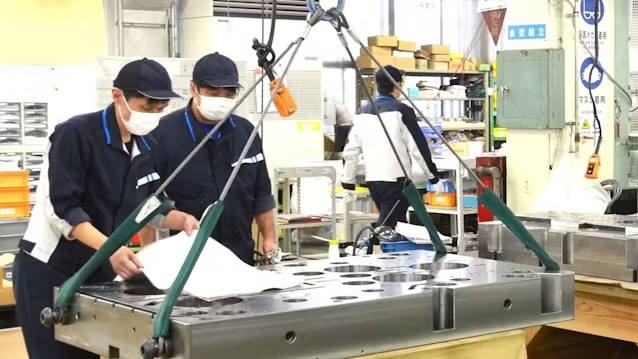
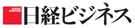
雄大な日本アルプスを間近に望むのどかな風土の長野県池田町。その一角にある黒田精工の長野工場は今、猫の手も借りたいほどの忙しさだ。
手掛けるのはモーターコア用の金型。コアは一見すると鉄鋼の塊をプレス機で成型しているように見える。だが、実は極薄の鋼板を1枚1枚プレス成型し、それを数百枚積層して作られている。
黒田精工は電気自動車(EV)駆動用モーターコアの金型で世界シェア3割を握る首位グループに名を連ねる。日米欧中の名うての自動車大手から受注を次々ともぎ取っており、足元では30を超す金型プロジェクトが走っている。
その最大の原動力は他社がまねできないブラックボックス化された技術にある。コアはプレスで薄板1枚1枚に微小な凹と凸を成型し、それを重ねて積層する作り方が一般的。
だが、黒田精工はプレス機内で薄板に接着剤を塗り、金型内で積層する技術を開発。これまでの作り方を一変させた。従来比で生産性を10%以上高めた上、より密着して積層できることから電気エネルギーを磁気エネルギーに変換する時に生じる損失を10〜20%低減。モーターのトルク(回転力)を17%向上させた。
しかも近年、軽量化のニーズから同等以上の磁気特性を保ちながら鋼板の厚さは0.25mmから0.2mm以下へと薄肉化している。
薄くなれば鋼板に凹凸をつけるのは極めて難しく、できたとしても歩留まりが悪い。だが、接着工法であればその心配も無用だ。
150度以上の耐熱性がある接着剤は化学大手と独自に共同開発し、塗り方やコアの品質に影響を与える金型温度の制御ノウハウなどを地道に追求。試行錯誤しながらコアの作り方を変えるだけでモーターの性能を格段に高めた。
そのイノベーション(技術革新)に真っ先に食いついたのは、名うての米EV大手だった。同社は常識をたたき壊すものづくりを好むとあって、工場を訪れたエンジニアは、安定量産できると見極めるや否や16年に採用を決めた。
それを起爆剤に黒田は拡販を進め、今では「接着積層が米EV業界のデファクトスタンダード(事実上の標準)になっている」(黒田精工の石井克則専務)といい、欧州の顧客にも次々と食い込む。
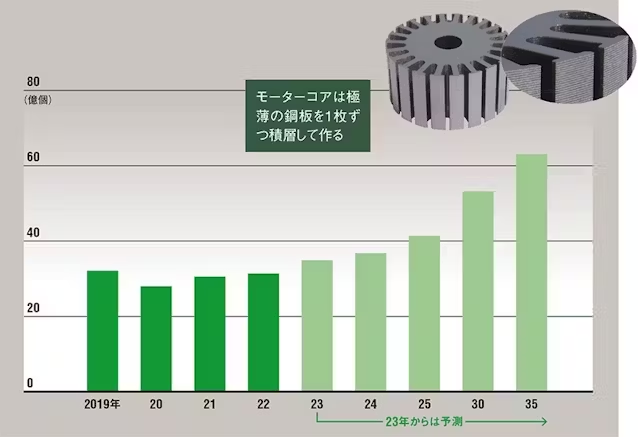
「デジタルに置き換わらない」
中国勢も追いかけてくるが特許は独占しており、ノウハウはブラックボックスだらけ。石井氏は「実用化できる技術として3年ほど中国は遅れている」と自信を示す。
コア用金型は精密そのもの。1マイクロ(マイクロは100万分の1)メートルの精度が要求される。このため最終段階では和紙のような専用の紙を金型に敷きプレスして精度を見極める。狙い通りでなければ金型を磨きながら微調整を繰り返す。
これができるのはエンジニアの技能継承のなせる業。「デジタルには決して置き換わらない」と黒田浩史社長は明言する。要素技術やすり合わせ技術を極めれば、エコシステムが守られ日本のものづくりが生き残れることを黒田精工は如実に示している。
黒田精工は10年前にコア世界最大手のユーログループ(イタリア)と提携。同社は欧米やアジア、メキシコと世界各地にコアの工場を持っており、最大顧客となっている。石井氏は「世界最大手なので完成車メーカーとの接点が多い。多種多様なモーターやコア設計の情報がどんどん入ってくる」と効果を語る。
24年初めに新工場が稼働したばかりだが、今後50億円を投じ、25年にも金型の生産能力を2.5倍に引き上げる計画だ。
世界シェア6割超、アイダエンジニアリングの「すり合わせ力」
ユーログループが食指を動かした日本企業は黒田精工だけではない。グローバル事業を動かす「車輪」の右が黒田精工とすれば左は高速精密プレス機世界大手のアイダエンジニアリングだろう。加圧能力300トン以上のコア用プレス機では世界シェアは65%前後とみられ、約30カ国に販売している。
自動車関連に強いが特にEV駆動用モーターコア向けの比率は急拡大しており、23年3月期は52%と初めて5割を超えた。プレス機はプログラムされた指示通りの位置で正確に動く・止まるを繰り返す「サーボモーター」が肝になる。
アイダは自社でモーターの開発、製作を進めている。モーターそのものにも精通していることから、顧客目線でプレス機を開発できる強みがある。同社のコア用プレス機は1分間に鋼板を360回打ち抜ける。600層のコアだと完成に2分もかからない計算だ。
プレス機には高速性と精密性が求められる。機械と金型との相性の良さがコアの品質を左右するとあって、相性は顧客が購入を決めるポイントとなる。
このため研究開発用に金型まで製作。サーボモーターから金型まで研究開発を垂直統合することで、ここでもすり合わせの妙が生かされている。モーターという完成品につらなるエコシステムの形成こそ、今の日本の強みだ。
山田ドビー、車載用モーターに活路
一世を風靡した「痛くない注射針」。ステンレス鋼板の微細加工を可能にしたのは、プレス機メーカーの山田ドビー(愛知県一宮市)の存在があった。1分間に2000回プレスする高速精密プレス機で世界シェアは4割程度とされる同社が活路を見いだすのもモーターだ。
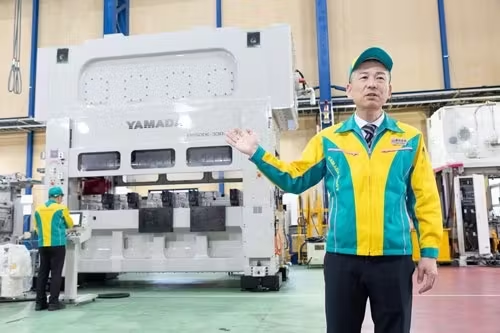
ブレーキやシート、パワーウインドーなど車1台当たり100〜150個のモーターが働いているが、各ユニットで電動化が進みモーターの搭載数は増えている。山田ドビーは車載用の中小型モーターに強い。コロナ禍で一時需要が縮小したものの、市場拡大に連動して回復。23年度の売上高は過去最高の水準に並んだ。
高速だが、10マイクロメートルのレベルで精密に圧力制御できる。これは細かな振動も吸収できる機械の構造設計(剛性)と、駆動機構が正確無比に動くものづくりの合わせ技。工場内には「工作機械のレクサス」ともいわれる安田工業(岡山県里庄町)製の高級マシニングセンターが並ぶ。プレス機部品の高精度加工に余念がない。
山田健雄社長は欧州のモーター市場を席巻しようと1年の半分以上はフランス・パリに在住。トップセールスで車関連メーカーへ売り込みを図る。「小回りの良さを生かしサプライチェーンに食い込んでいく」と藤村志郎取締役。増産投資も進めており当面、赤字先行でも供給力を高めるという。
黒田精工の黒田浩史社長に聞く
多種多様な引き出しを持ち、競合に勝つ
当社の強みは、80年ほどモーターコア用金型に特化しものづくりを続けていることだ。高度なすり合わせ技術が持ち味で1000分の1mmの精度で加工し、計測まで自前でやっている。
競合する中国の金型と比べコアの歩留まりや(金型の)耐久性で当社に一日の長があるが、脅威に感じているのはスピード。EVは進化が速い。新型のコアや金型の開発期間は通常3年だが、欧州メーカーは2年、米新興は1年、中国メーカーは6カ月という要求がくる。中国に対しては現地スピードに合わせるため試作を浙江省でやる体制を構築中だ。
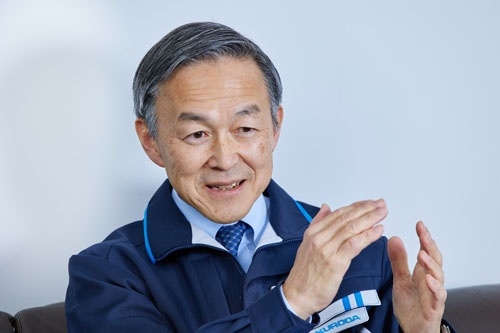
ユーログループは(コアを成型する)欧州やメキシコなどのプレス工場投資にアグレッシブ。その力もあって当社は金型を増産する投資を進めやすく、ある意味役割分担ができている。
コスト競争は激しくなっているが、カギは金型の大型化とみている。金型面積が広がれば1つの金型から1度のプレスで多数個のコアを取り出せる。材料の歩留まりも改善される。
ただ、大型化すれば金型の精度を出すのは難しい。設計も生産も創意工夫がいる。競合する中国企業に比べて技術優位性を保つことがこれからも欠かせない。(談)
(日本経済新聞 上阪欣史)
[日経ビジネス電子版 2024年4月12日の記事を再構成]
![]() |
日経ビジネス電子版
週刊経済誌「日経ビジネス」と「日経ビジネス電子版」の記事をスマートフォン、タブレット、パソコンでお読みいただけます。日経読者なら割引料金でご利用いただけます。 詳細・お申し込みはこちらhttps://info.nikkei.com/nb/subscription-nk/ |
鄭重声明:本文の著作権は原作者に帰属します。記事の転載は情報の伝達のみを目的としており、投資の助言を構成するものではありません。もし侵害行為があれば、すぐにご連絡ください。修正または削除いたします。ありがとうございます。